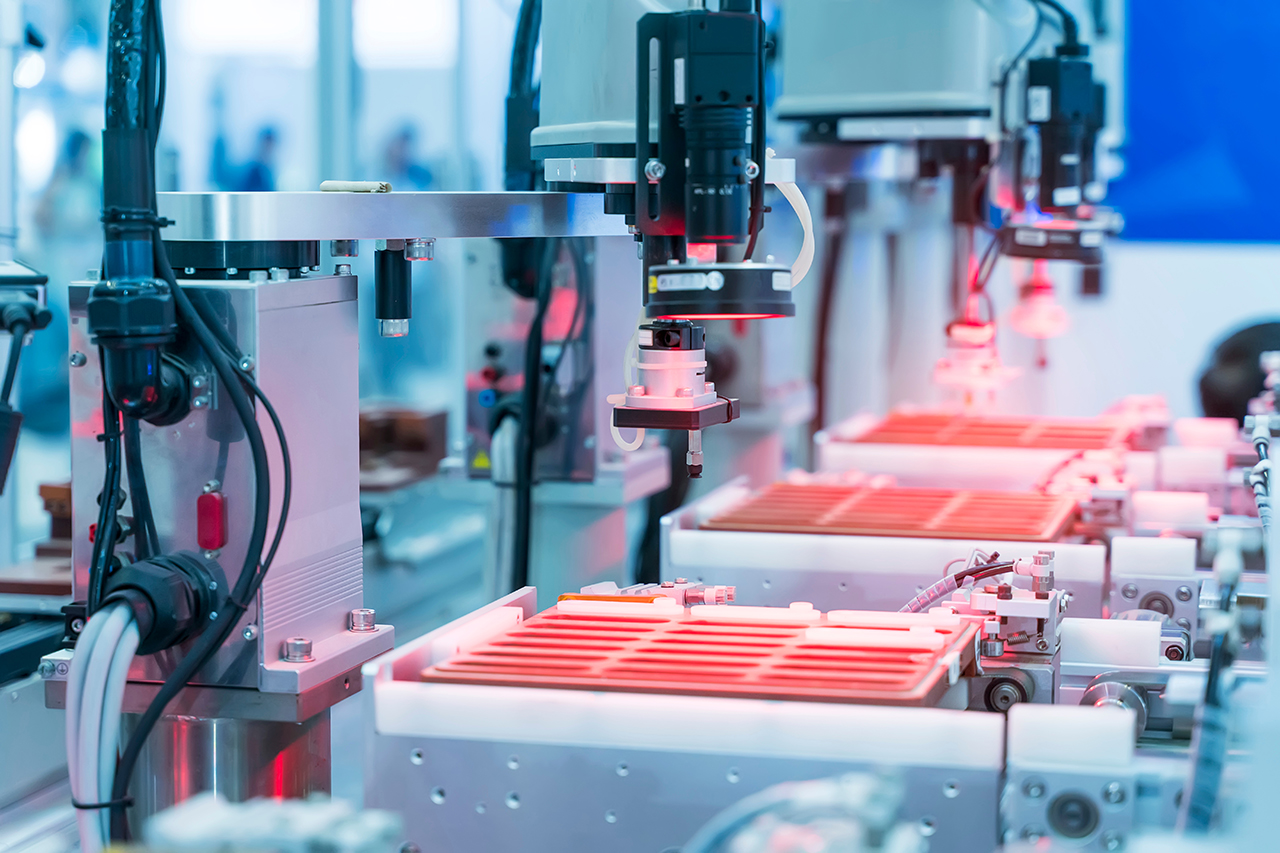
Jeff Dymond, Global CTO, Industries Edge and IoT
Manufacturing organizations who implement data-driven processes aided by computer vision are finding it easier to navigate uncertainties while staying ahead of demand. Diagnostic, proactive and predictive analytics from these intelligent camera systems are helping to maximize efficiencies to better ensure seamless production, distribution and aftermarket services even in the wake of unforeseen global events. In this article, we take a look at five key areas where computer vision is positively impacting manufacturing and the global supply chain, and how it will likely do so in the future.
Ever increasing advances in technology and continuous process optimization techniques have helped ensure that the global supply chain runs efficiently, turning raw materials into products that make their way to physical stores and ecommerce warehouses. However, we’ve witnessed how an outside disturbance like a pandemic or flood can fracture the supply chain, throwing businesses and consumers into temporary chaos. These disruptions are not necessarily due to a lack of product but more so to a lack of data. Where are the products within the supply chain at any given moment? How can they get to their destination when needed? When are there spikes in consumer demand and how much more of a product will be needed to meet that demand?
Quality is another important aspect of manufacturing. Whether you’re talking about components on a high-speed production line or levels in filling machines, every facet of the manufacturing industry focuses on quality detection and quality assurance. Maintaining high quality is difficult, even for experienced operators.
Manufacturers need to run their businesses out of the windshield, not the rearview mirror. A computer vision platform provides the ability to “see” and interpret in near-real time by gathering data at the edge and analyzing it at the right speed and velocity to make time-critical determinations and agile business decisions.
This forward-looking capability provided by computer vision is enabling manufacturing organizations to better address these top five business needs:
- How can we improve manufacturing personnel and facility safety?
For personnel, cameras look for personal protective equipment (PPE) use, such as hard hats and safety glasses, and then either send alerts to a manager if PPE is not being worn or gather data for forensic analysis that a safety officer uses to determine whether training is needed. Geofencing, creates a virtual boundary around equipment that’s hot to the touch or an area within reach of a robot; a loud alarm or flashing light is triggered when a person or object gets too close.
Repetitive movements is another safety issue that has long been a bane of manufacturing processes. Multiple repetitions of the same movement, such as when assembling a circuit board, can cause injuries in workers. Using cameras to study and optimize workflows often reduces the occurrence of employee injuries, promoting an overall safer workplace.
The use of thermal cameras in manufacturing is also on the rise to monitor objects for which sensors are not practical or to examine objects that are challenging for people to access in situ. For example, you can train a camera on conveyer system bearings to watch the change in temperature, ultimately producing a temperature histogram that shows the heat signature over time that is indicating a future failure. Thermography is also beneficial if visibility is needed in low light, such as for perimeter security in poorly lit areas.
- How can we increase manufacturing operational efficiencies today and what can we expect in the future?
Operational efficiency typically comes down to overall equipment effectiveness. If you’re not producing a quality product, you either have to throw it away or perform rework. An increase in production is required to make up for off-spec products to meet the product demand plan.
Consider a production line that uses automation technology, such as programmable logic controllers (PLCs) Cameras may be used to capture real-time streaming video images and thermal imagery of the production line and equipment.
A highly scalable computer vision platform would enable you to combine and aggregate the data, and then analyze the resulting data set to determine the cause of the off-spec product. Taking that a step further—with a computer vision platform leveraging a federated approach—the analysis happens in near real time as there would be no need to push large amounts of data back to a central storage location. This approach uses models at the edge to analyze data, sending only the results back to the central location for training and further refinement of the model (Figure 1). Then, only the updated model is sent back to the edge. It’s a much more efficient method of precisely and rapidly determining whether some piece of equipment or a part is running a little slower or a little hotter versus performing physical inspections.

“Figure 1. Moving to real-time situational awareness and insights. An example of a computer vision workflow where data capture, curation, movement, pre-processing, security archiving, data training and inferencing provide real-time insights at the edge.”
Other uses for computer vision include the ability to discern colors in the quality control process (is the potato chip a perfect light gold color or brown and overcooked?) and to find defects in parts that are difficult to view within larger assemblies. Thermography can gauge the levels of product in a tank, whether the product is crude oil in the field or soup in a factory, as well as the temperature of those tanks.
Looking to the future, predictive maintenance will be enhanced by computer vision technology, especially for equipment that needs to be in constant motion, shortening the time frame for replacements because scheduling can be done ahead of time and reducing overall costs for maintenance. Computer vision will be able to capture even more attributes from images and video, possibly replacing many sensors and transmitters used today. Also expect to see entire factories designed virtually, creating a digital twin with running processes that can be optimized before implementation.
- How can we positively impact the employee or “people” experience?
In the future, expect significant improvements to workday processes that currently require manual involvement and analysis. As an employee enters a factory, computer vision may recognize that person, recording the time they begin a shift (no need to punch a timecard) and automatically unlock doors to restricted areas. This also ties into safety. In case of an emergency, plant managers and first responders could get instant counts of the number of people in various locations. And augmented reality (AR) will enable much more flexibility in the types of skill sets required for certain jobs by pairing remote experts with lower skilled workers wearing cameras and interacting via AR.
- How can we affect sustainability in manufacturing?
One desired outcome of process optimization is a reduction in manufacturing consumption in relation to energy, chemical usage, air quality, and raw materials. Does a motor need to run 24/7? Maybe not, and a computer vision platform can look for patterns to determine when that motor should run and when it can be idle, which affects maintenance efforts and energy usage. The same principle applies to chemical usage, where optimized usage also means less over and under dosing. And using computer vision production quality reduces scrap that can’t be reworked and that has to go into landfills.
Cameras are also an efficient way to monitor stack emissions to reduce sulphur oxide (SOx) and nitrogen oxide (NOx) emissions by changing control parameters, and to check the color of water, such as in a reservoir, to determine the presence of pollutants or algae.
- How can we impact manufacturing revenue?
Business owners look at ROI, NPV and other metrics to justify the financials for doing a project or introducing a new product line. Computer vision in Manufacturing is used to increase revenue, reduce costs, and increase worker safety. An example of maximizing revenue is through maximizing first-pass quality which increases yield or a reduction in scrap which saves money in raw materials. Furthering the sustainability discussion, a reduction in energy, or chemical usage also lower costs.
Although some aspects of computer vision have been in use in manufacturing for years, real-time data analytics is having the biggest impact. With more plants embracing computer vision for quality assurance, plant visibility, equipment monitoring, and worker safety, it’s possible to envision a global supply chain in the future that can better react to outside disturbance variables and continues to operate smoothly under almost any circumstances.
For an overview of computer vision and its impact on manufacturing, see Delivering game-changing Production Quality with Computer Vision.
Learn more about how Computer Vision is positively impacting other industries:
- The Future Is Computer Vision – Real-Time Situational Awareness, Better Quality and Faster Insights
- Computer Vision Is Transforming the Transportation Industry, Making It Safer, More Efficient and Improving the Bottom Line
- How the Sports and Entertainment Industry Is Reinventing the Fan Experience and Enhancing Revenues with Computer Vision